MCX W: Bluetooth LE, Zigbee, and Matter over Thread multiprotocol MCUs
Different Types of Sensors and Sensing Technologies
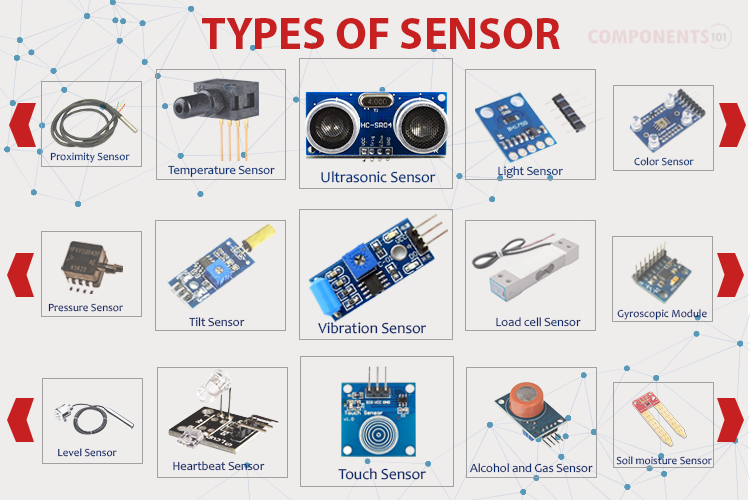
What is a Sensor?
A sensor is a device that can detect a change in its surrounding environment and provides output in the form of an analog or digital signal, which is then either displayed or can be used by a closed-loop system for process control. For better understanding, we can say that a sensor is a device that can see, hear, feel, smell, and taste its surroundings and probably do it better than me or you (obviously it depends on the make and quality of the sensor). Sensors are usually connected to a transmitter because the output of the sensor needs to be conditioned or amplified since the output is very small. Hence, a sensor requires other equipment for us to utilize the data, and more often than not we call the whole package as a sensor. In this article, I will be writing about some common sensors available in the market, I will be giving you brief information about those sensors and will also tell you about their applications in the real world.
Classification of Sensors
In process control, there are two types of sensors as mentioned below: Active and Passive Sensors Passive sensor requires an external source of power to work. For e.g. a thermistor, Light resistor, strain gauge, etc. While an active sensor doesn’t require any external source of power. For e.g. a Piezo electric, thermocouple, etc.
Analog and Digital Sensors
The analog sensor gives output in the form of analog output when it detects changes in external parameters (wind speed, solar radiation, light intensity, etc.). An analog sensor with an output range of 0 to 5V can give the output anywhere between 0V and 5V.
Unlike analog sensors, Digital sensors produce discrete values (0 and 1’s). Discrete values are often called digital (binary) signals in digital communication.
Logic High is treated as “1” whereas Logic Low is indicated by “0”.
Difference between Sensor and Transducer
Before diving into the different types of sensors, the first thing that we should know is the difference between the sensors and the transducers.
A sensor is a module or chip that observes the changes happening in the physical world and sends the feedback to the microcontroller or microprocessor. As shown in the figure above, excitation (Power supply) and Grounding must be provided to the sensor for proper working.
A transducer also observes the changes happening in the physical world, but unlike a sensor, it doesn’t require power, it measures the change and converts it into the form of voltage output. There are two kinds of transducers, input transducers take energy or measurement in a form and convert it into electricity, for e.g. a microphone. Whereas an output transducer takes electrical energy and converts it into another form of energy, for e.g. a speaker.
Different Types of Sensors
In today’s time, there are multiple sensors for detecting different parameters and measuring different characteristics of the physical world. Many of the sensors can be utilized in detecting data in different scenarios. For example, an ultrasonic sensor can be used for detecting distance, speed, temperature, etc. just by using different calculations from its acquired data. Therefore, sensors can be classified into different parameters. Sensors can be classified based on the physical parameter it sense, they can also be categorized based on the applications, or by the industry they are being used. So, in this article, I’ve classified the sensors based on their most prominent usage.
Some common types of Sensors are:
- Temperature Sensors & Thermocouple Sensors
- Proximity Sensor
- Ultrasonic sensor
- Pressure Sensor
- Hall Effect Sensor
- Load cell
- Light Sensor
- Color Sensor
- Touch Sensor
- Tilt Sensor
- PIR Motion Detector & Vibration Sensor
- Accelerometers & Gyroscope Sensor
- Metal detector, Water Flow & Heartbeat Sensor
- Flow and Level Sensor
- Gas and Alcohol Sensor
- Humidity and Soil Moisture sensor
Temperature Sensor
Temperature sensors are used for measuring the temperature of any object or medium. Temperature is a fundamental measurement of thermal energy which has an SI unit in Kelvin. It is one of the most widely used sensors. The majority of these are contact sensors while infrared and ultrasonic temperature sensors are contactless sensors.
Temperature Sensor types
Temperature sensors come in both analog and digital types. The most commonly used temperature sensors are thermocouples, thermistors, and RTDs.
Thermocouples:
These are the most commonly used type of temperature sensor. They are made by joining two dissimilar metal wires together and work on the principle of the Seebeck Effect. Thermocouples are preferred because they are self-powered and require no excitation while working over a wide temperature range.
Usage - These sensors are used in industrial, automotive, and consumer applications.
RTDs:
The resistance temperature detector also known as RTD works on the principle that the resistance of metals is affected by their temperature. RTDs are commonly made up of platinum, nickel, or copper wires, due to their positive temperature coefficient, i.e., the rise in temperature results in an increased resistance – the change of resistance is then used to detect and measure temperature changes.
Thermistors
Similar to RTD, thermistor also measures the change in resistance to measure temperature, but unlike RTD thermistors are made up of ceramic or polymer materials. Mostly thermistors are cheaper but are also less accurate than RTDs. Most thermistors are available in two-wire configurations, NTC (Negative Temperature Coefficient) and PTC (Positive temperature coefficient). The NTC have an inverse relationship with the temperature, i.e., with an increase in temperature the resistance increases and with a decrease in temperature resistance increases whereas in the PTC the resistance increases with an increase in temperature and vice versa. PTCs are more commonly used as fuse. Some common thermistors are shown in the image below.
Some other kinds of temperature sensors are:
- Thermometers
- Vibrating Wire Temperature Sensors
- Infrared temperature sensor
- Ultrasonic temperature sensor
Temperature Sensors Application
Thermal sensors are widely used for temperature measurement in medical applications, power electronic circuits, battery packs, computers, aerospace applications, automotive applications, environmental monitoring, etc.
Proximity Sensors
Proximity sensors are sensing devices capable of detecting the presence of objects without physical contact. These are among the most commonly used sensors. There are different kinds of proximity sensors depending on the physical quantity they measure. If you wanna learn more about proximity sensors and their types you can check out the linked article.
Types of Proximity Sensors
- Inductive proximity sensors
- Magnetic proximity sensors
- Capacitive proximity sensors
- Photoelectric proximity sensors
- Ultrasonic proximity sensors
Proximity Sensors Application
It is most commonly used in industries to measure the close proximity of any mechanical parts, in mobiles, proximity sensors are used for the detection of faces during calls. They are used in safety systems and in the automotive, aerospace industry etc.
Position Sensors
Position sensors are devices that can detect the movement of an object or determine its relative position measured from an established reference point. These types of sensors can also be used to detect the presence of an object or its absence. Position sensors are sometimes confused with proximity sensors. Although both these sensors are very similar to each other, in fact, all the proximity sensors can be considered as position sensors, the main difference is that the position sensor gives the exact position of an object, whereas the proximity sensor only talks about the presence or absence of an object in an area.
There are several sensor types that serve similar purposes to position sensors, and which are worthy of mentioning. Motion sensors detect the movement of an object and can be used to trigger actions such as turning on a light and fan automatically or activating a security camera. Proximity sensors as well can detect that an object has come within range of the sensor. Both sensors, therefore, might be considered as a specialized form of position sensors.
Position sensors are capable not only of detecting any object but also of measuring and recording the position and therefore involve the use of a feedback signal that contains positional information.
- Different types of Positional Sensors are
- Potentiometric Position Sensors (resistance-based)
- Inductive Position Sensors
- Eddy Current-Based Position Sensors
- Capacitive Position Sensors
- Magnetostrictive Position Sensors
- Hall Effect-Based Magnetic Position Sensors
- Fiber-Optic Position Sensors
- Optical Position Sensors
- Ultrasonic Position Sensors
The two most common types of position sensors are the Hall effect and ultrasonic sensors.
Ultrasonic Sensor
This sensor uses ultrasonic waves to detect any object in its path. It has a transmitter and a receiver which are made of piezoelectric crystals. The transmitter produces the ultrasonic waves and the wave hits the object and returns back to the same path which is detected by the ultrasonic receiver. The ultrasonic sensor utilizes the time of flight (TOF) technique to measure the distance of the object. Ultrasonic waves travel faster than the speed of audible sound (i.e. the sound that humans can hear).
In order to calculate the distance between the sensor and the object, the sensor measures the time it takes between the emission of the sound by the transmitter to its contact with the receiver. The formula for this calculation is D = ½ T x C
Here, D is the distance between the transmitter and the object, T is the time, and C is the speed of sound ~ 343 meters/second.
The image below shows an HC-SR04, which is one of the most widely used ultrasonic sensors by hobbyists. It has both transmitter and receiver in a single module.
Application
These sensors are mostly used to detect objects, and measure distance and can also be used for measuring temperature, pressure, fault in structure or material, etc.
Hall Effect Sensors
A Hall effect sensor is a type of device that detects magnetic fields. It operates based on the Hall effect; a phenomenon discovered by Edwin Hall in 1879. The basic principle is that when a conductor or semiconductor with current flowing in one direction is introduced to a perpendicular magnetic field, a voltage (the Hall voltage) can be measured at right angles to the current path. Hall effect sensors are widely used for proximity sensing, positioning, speed detection, and current sensing applications. The output signal from a Hall effect sensor is the function of magnetic field density around the device. When the magnetic flux density around the sensor exceeds a certain pre-set threshold, the sensor detects it and generates an output voltage called the Hall Voltage, VH. The Hall effect sensor has various applications but is mostly used in position detection.
Depending on the output signal the hall effect sensors can be either an analog one or a digital one. They can also be classified into two new groups unipolar and bipolar. The unipolar hall effect sensors can only sense one magnetic pol while the bipolar can detect both magnetic pols.
Positional Detector
Positional detectors are sensors which are used to detect the position of any object, they can be made using distance sensors such as ultrasonic sensors or by using proximity sensors such as hall effect sensors etc.
Some other kinds of positional detectors are:
1. Head-on Detection
As its name implies, “head-on detection” requires that the magnetic field is perpendicular to the hall effect sensing device and that for detection, it approaches the sensor straight on towards the active face. A sort of “head-on” approach
2. Sideways Detection
The second sensing configuration is “sideways detection”. This requires moving the magnet across the face of the Hall effect element in a sideways motion.
This head-on positional detector will be “OFF” when there is no magnetic field present, (0 gauss). When the permanent magnet's south pole (positive gauss) is moved perpendicular towards the active area of the Hall effect sensor the device turns “ON” and lights the LED. Once switched “ON” the Hall effect sensor stays “ON”.
Positional Detectors Application
Positional detectors are widely used in assembly lines to measure position and send feedback to the control system, it's also used in engines to detect the position of the crankshaft for proper combustion.
Load Cell
A load cell is a transducer that converts mechanical force into an electrical signal. This conversion enables the measurement of physical forces like pressure, tension, compression, or weight. Load cells are essential components in scales, industrial systems, and various types of sensing equipment, providing accurate measurements of force or load.
Here’s how a load cell typically works:
The core of a load cell is usually made of steel or aluminum, where the material is shaped to have one or more regions that deform when a load is applied. This deformation is tiny and not usually visible to the naked eye. Attached to the deforming region are strain gauges, which are thin, conductive patterns that change their electrical resistance when stretched or compressed. Most load cells use four strain gauges in a Wheatstone bridge configuration, which maximizes the output signal and provides temperature compensation.
When a load or presssure is applied to the cell, the strain gauges deform slightly. This deformation changes their electrical resistance. The Wheatstone bridge converts this change into a measurable voltage change, which is proportional to the force applied.The electrical signal from the strain gauges is usually very small. Therefore, it often goes through an amplifier to increase its magnitude, making it easier to measure and interpret. This amplified signal can then be converted from analog to digital form if needed for further processing by digital equipment. The output signal is calibrated to ensure accuracy. The calibration process involves applying known loads to the load cell and adjusting the measurement output to match the applied load accurately. The final output can be displayed on a monitor, stored for future reference, used to trigger an action, or further processed as required.
Load cells are widely used in various applications, including weighing scales, industrial automation systems, testing equipment, and safety testing devices. They come in different shapes and sizes, each designed for specific types of loads, ranges, and accuracy requirements. Some common types include single-point load cells for scales, shear beam and bending beam load cells for industrial weighing, and compression load cells for heavy-duty applications like truck scales and silo weighing. Load cells come in various shapes and designs, each tailored for specific applications. Here's a brief overview of the types you mentioned:
- Button Load Cells: These are compact, low-profile load cells used in applications where space is limited. They are ideal for measuring compressive loads and are often used in medical devices, clamping forces, consumer product testing, and embedded applications. Button load cells can provide high accuracy and are designed to handle off-center loads effectively.
- Donut Load Cells: Also known as through-hole load cells, these are designed with a central hole and are typically used in applications where the load or force must pass through the center. They are ideal for bolt force measurements, clamping forces, and overload monitoring. Donut load cells are often used in applications where the load cell must be integrated into a bolted joint or where limited space is available around the loading point.
- S-Type Load Cells: Named for their S shape, these load cells are versatile devices that can measure both tension and compression loads. They are commonly used in hanging scales, crane scales, hopper scales, and various mechanical-to-electronic scale conversion projects. S-Type load cells are popular due to their flexibility in installation and their ability to handle a wide range of weight capacities.
- 3-Axis Load Cells: These load cells are capable of measuring force in three directions: X, Y, and Z axes. This allows them to measure forces and moments applied in all three spatial dimensions, making them ideal for applications where multi-axis force measurement is required, such as robotic assembly, testing and analysis of mechanical systems, and aerospace testing. They can provide detailed information about the forces and moments exerted on an object, enabling precise control and monitoring of complex systems.
Each type of load cell is designed to meet specific requirements in terms of load capacity, precision, and application environment. Choosing the right load cell depends on the specific needs of your project, including the range of forces to be measured, the environmental conditions, the required accuracy, and the physical space available for the load cell installation.
Potentiometer Sensors
It is a contact-type sensor which measures the distance or displacement of an object in linear or rotary motion respectively and provides an electrical output. It is of 3 types used for detecting different positions of movement. It uses the same principle as a potentiometer used for changing the flow of current in an electric circuit.
Inductive Position Sensor
Inductive position sensors use the physical principles of induction in a wire loop and eddy currents to detect the position of a solid metallic structure that is sliding or rotating above a set of coils consisting of one transmitter coil and two receiver coils.
Capacitive Sensor
Capacitive sensors are designed for non-contact measurement of displacement, distance and position, as well as for thickness measurement. Due to their high signal stability and resolution, capacitive displacement sensors are applied in laboratories and industrial measurement tasks.
Position Sensors Application
Position sensors are widely used for machine tools, robotics, motion systems, material handling, hydraulic control, steering, braking, etc.
Accelerometers & Gyroscope Sensor
The accelerometer sensor is used to measure the acceleration of a body in any direction while the gyroscope measures rotational velocity or rate of change of the angular position over time, along the X, Y and Z axis. These sensors are used in combination to detect the velocity of an object. A commonly used gyroscope with Arduino is the MPU6050 module.
Gyroscope and Accelerometer Sensor Applications
Some of the common applications of these sensors are optical Image stabilization used in camera lenses, Gesture-Based Control, Navigation, movement detection in mobile phones and other devices, etc.
Pressure Sensor
These sensors are used to measure the force exerted on a body or in an environment due to solid, liquid or gaseous objects. Pressure = Mass/Unit area. Similar to pressure sensors there are pressure gauges. Pressure gauges by their design provide a direct output reading of a pressure value referred to as gauge pressure. Pressure sensors can be classified into absolute pressure, gauge pressure and differential pressure. Gauge pressure is measured relative to the atmospheric pressure whereas absolute pressure is measured relative to a vacuum, whereas the differential pressure is a measurement of the pressure difference between two points.
The above image shows a BMP085, a commonly used barometric pressure sensor from Bosch.
Different types of Pressure measurement are:
- Differential Pressure
- Absolute Pressure
- Guage Pressure
Types of Pressure Sensor
- Potentiometric pressure sensors
- Inductive pressure sensors
- Capacitive pressure sensors
- Piezoelectric pressure sensors
- Strain gauge pressure sensors
Pressure Sensor Applications
Pressure sensors are used to measure the pressure exerted on any object or at any point, it can also be used to indirectly measure other variables such as fluid/gas flow, speed, water level, and altitude.
Vision and Imaging Sensors/Detectors
As the name suggests, vision and imaging sensors and detectors detect the presence of any object or colour within its field of view. The detected input is converted into a digital image for display. The sensor module usually has a camera, lights and controller in it. These sensors are used in manufacturing plants and assembly lines to detect any fault in the manufacturing process by sensing presence, positioning and abnormality, also they are used in present-day cars to ease the reversing of vehicles for the driver.
Light Sensor
Light sensors also known as Photoelectric Devices or Photo Sensors convert light energy (photons) into electronic signals (electrons). Photoelectric sensors use light to detect the presence or absence of an object. It emits a light beam (visible or infrared) from its light-emitting element. A reflective-type photoelectric sensor is used to detect the light beam reflected from the target. A beam of light is emitted from the light-emitting element and is received by the light-receiving element. Both the light-emitting and light-receiving elements are contained in a single housing. The sensor receives the light reflected from the target. Some different types of light sensors are shown in the image below:
The most common types of light sensors used are Phototransistors, photoresistors, and photodiodes.
A Photoresistor, more commonly known as LDR are resistors whose resistance is dependent on the intensity of light. The resistance is inversely proportional to the intensity of the light, i.e. the resistance is higher in a dark room compared to the resistance of LDR in a bright room.
A Phototransistor is an electronic switching and current amplification component which relies on exposure to light to operate, in easier words, phototransistors are a type of transistors that convert light energy into electrical energy, and the output is dependent on the light intensity.
A Photodiode is a semiconducting device which generates electric current when light falls into it. The main difference between a photodiode and a photoresistor is that a phototransistor only produces current while a photoresistor or Light-dependent resistor’s resistance is dependent on the intensity of light falling on it.
Light Sensor Application
Light sensors are used in security systems, ambient light detection, and object detection and have applications in Industries, automobiles, military and are extensively used by almost all in everyday lives.
LIDAR Sensor
Light Detection and Ranging also known as LIDAR is a common technique of measuring distance. It works by emitting light which hits an object in its path and travels back on its original path which is then detected by the receiver, giving an exact measurement of the distance. The below pic shows a VL53L0X – Lidar sensor, which was also used in the iPhone 7 for 3D imaging.
Applications of Lidar Sensor
LIDAR is widely used in camera autofocus to enhance in the camera performance in low light or fast-moving objects conditions, it is also used as a proximity sensor in many phones. LIDAR also finds its application in advance usage in oceanography, terrain modeling of Earth’s surface, Automobile and Aerospace industry, etc.
PIR Sensor
The passive infrared sensor more commonly called a PIR sensor detects the Infrared light radiating from a body. It uses a pair of pyroelectric sensors to detect heat energy in the surrounding environment. It uses a pair of pyroelectric sensors to detect heat energy in the surrounding environment. These two sensors sit beside each other, and when the signal differential between the two sensors changes (if a person enters the room, for example), the sensor will engage. The PIR sensor can have range from 0.25m to 150m.
Application of PIR Sensor:
These are used to detect motions, it can be used for theft detection, pedestrian detection, etc.
Color Sensor
A color sensor is used to detect the color of a material. it emits a light on an object and detects the reflected light to measure the intensity of red, blue and green light reflecting back from the sensor. These sensors are also equipped with filters to reject unwanted IR light and UV light. An image of TSC3200 which is extensively used by enthusiasts in DIY projects is shown below.
Color Sensor Types
There are 2 types of color sensors, 1 emits red, blue and green lights independently and measures the intensity of each light while the other type of sensor emits a broad spectrum of light and detects the light falling onto it. TCS3200 is a commonly used sensor working on the broad spectrum of light method.
The colour is detected by the presence or absence of either of the lights based on the table below:
Application of Color Sensor
Colour sensors are commonly used in the automobile industry, textile industry and other manufacturing industries to detect the colour of the product. It is also used in cameras to detect the surrounding colour to adjust the lighting conditions.
Touch Sensor
Touch sensors also known as tactile sensors are used for detecting or recording physical touch. They work by either allowing or changing the flow of current in the circuit. These sensors are widely used as switches or are embedded in displays to make displays register a command.
Types of Touch Sensors
There are different types of touch sensors such as resistive touch sensors, capacitive touch sensors, Infrared touch sensors, surface acoustic touch sensors etc. The most common types are resistive and capacitive touch sensors which are described below:
Resistive Touch Screen
Resistive touch sensors are the simplest sensors which have 2 layers of electrically resistive sheets, separated by a layer of inert gas or air. The pressure from touch results in both the sheets coming in contact with each other thus causing the voltage to change which is interpreted by a circuit. These are mostly found in early smartphones and other touch panels such as touch music instruments and touch cable handheld devices.
Capacitive Touch Screen
Similar to resistive touch screens, these touch screens have 2 layers of conductors with an insulator between them. The whole setup acts as a capacitor, when our finger which acts likes a conductor comes in contact with the sensor, the capacitance of the point increases. A capacitance measuring circuit continuously measures the capacitance and when it observes the change in capacitance, it generates a signal. These touch sensors are most commonly used in the latest smartphones. These are used in smartphones, electronic watches, game consoles, industrial control equipment, touch pads, etc.
Application of Touch Sensors
Touch sensors are used as switches in homes, commercial buildings, automobiles, etc. These are embedded into displays of portable devices such as phones, TV screens or other handheld devices.
Gas and Chemical Sensors
These sensors are used to detect the presence of different types of gasses and their concentration present in the atmosphere. They are commonly used to detect toxic or explosive gasses and measure gas concentration by changing the resistance value. A detailed explanation of gas sensors can be found here. MQ2 gas sensor is widely used for detecting methane, butane, LPG and smoke.
Different Types of Gas sensors
Gas sensors are typically classified into various types based on the type of sensing element it is built with. Below is the classification of the various types of gas sensors based on the sensing element that are generally used in various applications:
- Metal Oxide-based gas Sensor.
- Optical gas Sensor.
- Electrochemical gas Sensor.
- Capacitance-based gas Sensor.
- Calorimetric gas Sensor.
- Acoustic-based gas Sensor.
Application of Gas Sensors
Gas sensors are employed in factories and manufacturing facilities to identify gas leaks, and to detect smoke and carbon monoxide in homes.
Humidity Sensor
A humidity sensor also known as a hygrometer is a sensor used for measuring humidity in air. It senses and measures both moisture and air temperature. The ratio of moisture in the air to the highest amount of moisture at a particular air temperature is called relative humidity. Humidity sensors work by detecting changes that alter electrical currents or temperature in the air. DHT11 is a commonly used humidity sensor.
Types of Humidity Sensor
- Capacitive
- Resistive
- Thermal
Application of a Humidity sensor
Used for measuring humidity in homes, offices, granaries, manufacturing plants, storage rooms, humidors, museums, industrial spaces and greenhouses and are also used in meteorology stations to report and predict the weather.
Radiation Detectors
Radiation sensors measure the amount of radiation emitted from a body. There are different sensors which can be used to measure different kinds of radiation such as nuclear, electromagnetic and light. The different particles that can be measured are Alpha particles, Beta particles, Neutrons, X-rays and Gamma rays. The low-cost detectors have a gas-filled tube with a wire at a very high voltage which is used for collecting the ionization produced by the incident radiation. However this method is unable to distinguish between different kinds of radiation.
The most common types of Radiation Detectors are:
- Gas-filled radiation detectors
- Scintillation radiation detectors
- Solid-state radiation detectors
Application of a Radiation Detector
These sensors can be used to measure radiation from a body in a nuclear power plant or to see if an area is safe or not.
Commonly Used Sensors in IoT
Sensors are a very important and integral part of any IoT device. All of them depend on different sensors to properly operate. If you wonder what are the most commonly used sensors in electronics here are few example. Temperature sensors like the DS18B20 and LM35 are ubiquitous for monitoring climate conditions, essential in smart homes and industrial systems. Humidity sensors, such as the DHT11 and DHT22, are key for managing air quality and comfort. Pressure sensors, like the BMP280 and MPX5010, find their place in everything from weather stations to health monitoring devices. Proximity sensors and light sensors are fundamental in automating systems, controlling lighting, and enhancing user interfaces, whereas motion sensors like PIR are standard in security and energy-efficient lighting solutions. Gas sensors are crucial for safety and air quality monitoring, detecting harmful or combustible gases. Accelerometers and gyroscopes are widely adopted in smartphones and vehicles for navigation and stability control. Ultrasonic sensors are typically used in distance measuring or obstacle detection. These sensors collectively form the backbone of IoT, providing data that enables smarter decision-making and automation in various applications.
Popular Sensors
Here are some of the popular sensors available in the market.
Sensor Type | Popular Examples/Parts |
Temperature Sensors | LM35, DS18B20, TMP36, SHT20, AHT20, LM335,PT100s |
Proximity Sensor | LJ12A3, VL53L0X, E18-D80NK, TCRT5000,PR12-2DN, CR18-8DN |
Ultrasonic Sensor | HC-SR04,MB1040, US-100, A02YYUW,MB1001,MB7052,URM09,URM-37 |
Pressure Sensor | BMP280, MPX5010, HX711,HX701B, WPAH01, MPX10DP |
Hall Effect Sensor | A3144, SS495A, OH090U, DRV5032, WSH49E, AH180 |
Load Cell | DYMH-103, SEN-10245, TAL220, TAL221, YZC-133, YZC-131 |
Light Sensor | BH1750, LDR (Light Dependent Resistor), TSL2561 |
Color Sensor | TCS34725, TCS3200, ADJD-S311,TEMT6000, TSC34725, TSL25911 |
Touch Sensor | TTP223, TTP224, TTP226, TTP229, MPR121, MTCH101, CAP1298, CAP1203, AT42QT1012 |
Tilt Sensor | RPI-1031, SW-520D, SW420, AT407 |
PIR Motion Detector | HC-SR501, HC-SR505, AM312, ZRD-09, D203S, EKMB1306112K |
Vibration Sensor | SW-420, SW18020P, ADXL345, 801S, TPSW-200M |
Accelerometers & Gyroscope Sensor | MPU-6050, ADXL345, LSM9DS1, MPU9250, ADXL356, MPU6500 |
Metal Detector | A88, LJ12A3 |
Water Flow Sensor | YF-S201, FS300A, G1/2 Water Flow Sensor, SEN-HC21WI, SEN-HCG1WA, YF-DN50, YF-S401 |
Heartbeat Sensor | MAX30100, MAX30102 |
Flow and Level Sensor | XKC-Y25, XKC-Y25, FS-IR02, P43, YW517B1 |
Gas and Alcohol Sensor | MQ-2, MQ-3, MQ-4, MQ-5, MQ-6, MQ-7, MQ-8, MQ-9, MQ-131, MQ-135, MQ-136, MQ-137, MQ-138,MQ-214 |
Humidity and Moisture Sensor | DHT11, DHT22, Soil Moisture Sensor (Capacitive/Resistive), AHT-25, SHT20 |
Conclusion
A sensor is capable of detecting physical changes in our surroundings. Many sensors are capable of giving multiple data and thus can be used in multiple applications. A capacitive sensor can be used as a touch sensor or be used for object detection, position detection, etc. Different accuracy and resolution of sensors are required for different applications and the selection of sensors is usually based on the desired accuracy, speed and resolution of data.