MCX W: Bluetooth LE, Zigbee, and Matter over Thread multiprotocol MCUs
A Guide to Choosing the Right SMPS Power Management Controller
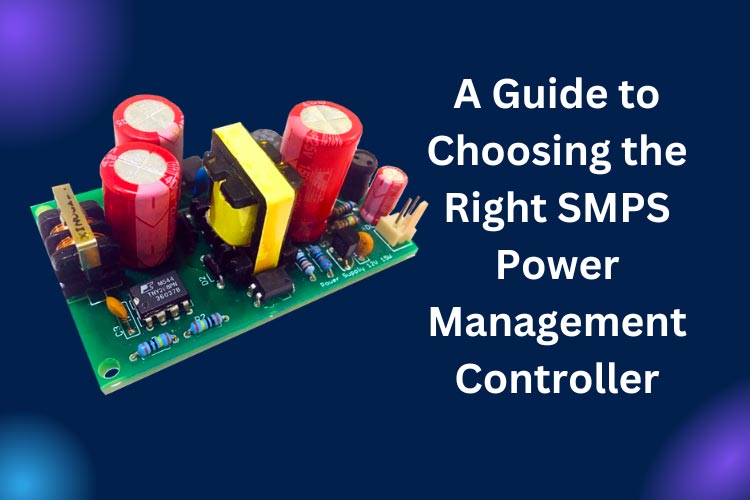
Power supplies are an important part of any electronic system. Even though there are multiple categorizations within the power supplies, we are going to look into the AC- DC converters, that are used in mains powered equipment and appliances. In the AC-DC power supplies the Switch Mode Power Supplies (SMPS) are the preferred type due to their efficiency and smaller size compared to the traditional linear power supplies such as transformer based, or capacitor dropper based once. The controller circuit in an SMPS is the critical section within it that will greatly affect the performance and efficiency of the power supply. Nowadays everything is integrated and that goes to the SMPS control circuit too. There are dedicated controller chips, specially designed for the purpose. They are responsible for different operations such as voltage and current regulation, primary and secondary switching, and even power factor corrections. In this article, we will provide a guide for selecting the appropriate SMPS Control ICs for your applications. We will cover the basic selection criteria for such controllers, and we will also discuss some of the most popular choices within the industry and the maker community.
First, it is important to understand the basics of how an SMPS controller ICs works. These ASIC controller chips regulate the output voltage and current using PWM or Pulse Width Modulation. They are typically operating in a closed-loop feedback system, by constantly monitoring the output voltage and current, while adjusting the pulse width to maintain the desired output voltage. Some are even capable of adjusting the switching frequency to get better performance.
When selecting an SMPS controller IC there are several factors that must be considered:
-
Input Voltage Range: The first and very important specification is the input voltage range. There are several types of SMPSs are available in the market, some are universal, some are specifically designed for a specific market. For example, an SMPS designed for Indian market is only needed to operate with an input range of 165-260V AC. But we can’t use them in countries with 110V AC lines. They will need specific SMPS, or we may need to use Universal SMPSs that will work even from 80v AC. Then you might think why we don’t just make everything universal. While the universal power supplies are convenient to use, they may have some disadvantages compared to the market specific once such as reduced efficiency. So, it is important to consider the actual need.
-
Output Voltage and current: The output voltage and current must be with in the needs of our application. The controller must be able to regulate the output voltage and current effectively without compromising the efficiency and must not exceed the output noise level. For controllers with built in switching transistors, the output values must keep within its limitation to ensure the smooth and failure free operation.
-
Output Ripple: The output ripple is the voltage noise or ripples at the output created due to the switching operations. They must be below the allowed level. The allowed level will be dependent on the applications. For example, for consumer applications the allowed voltage ripple will be higher than the industrial or medical application. The voltage ripple may affect critical equipment for critical applications. So, it is important to keep the ripple to a bare minimum as much as possible.
-
Switching Frequency: The switching frequency can affect multiple characteristics such as over all size of the external components, efficiency etc. We can use smaller components if we use higher frequency. But the higher frequencies can affect the applications specific circuits that we are powering. And it can also greatly affect the efficiency of the power supply. So, it is important to choose the controller with the optimal switching frequency for our application.
-
Package type: The package type of the controller chip is also important. It can affect the built cost and structural properties. Different package types will have different pin configurations and dimensions. Choosing an incorrect package type can cause layout issues and increase in cost. It can also affect the repairability and size of the final product too.
-
Protection features: The controller should have appropriate protection feature to protect the applications circuit against conditions such as overvoltage, over current and over temperature. If we have external protection, we can choose the controller with minimal protection which may help reduce cost. But sometimes it may be in reverse. So, it is important to choose the one with our needs.
-
Cost: Finally, the cost is important factor. Especially in consumer production. We can’t always just opt for the higher end components, they might have additional features and better performance, but they may also be more expensive. So, we must always find a balance between the cost and the features we get.
So in conclusion, it is critical to select the appropriate controller C for the proper operation of the power supply and the end product. By considering the above mentioned points, we can select the controller chip that is best for our application and meets our requirement.
Now let’s look at some of the popular controller chips in the market and their features:
UC3842/43/44/45
The UC3842/43/44/45 are fixed frequency current-mode PWM controllers. They are designed specifically for Off-line and Dc-Dc converter applications with minimal external components. They features trimmed internal oscillator for precise duty cycle control, internal temperature compensated voltage reference, high gain error amplifier, current sensing comparator and high current totem pole output for driving power MOSFET. They also features built in Under Voltage Lockout(UVLO) and current limiting for protection. While the UC3842 and UC3844 have a UVLO thresholds(on/off) of 16V/ 10V, and the UC3843 and UC3845 have a UVLO thresholds(on/off) of 8.5V/ 7.9v. The UC3842 and UC3843 has a maximum duty cycle of 100% while for UC3844 and UC3845 it is 50%. They operate at a fixed frequency of 500KHz, and a gate drive current of 1A with a power dissipation of 1W.
The UC344X family controllers also offers features such as pulse-by-pulse current limiting, enhanced load-response characteristics, low start-up current(<1mA), Automatics feedback compensation, double-pulse suppression, and undervoltage lockout with hysteresis. They are available in PDIP 8, SOIC 8 and SOIC 14 packages.
TL494
TL494 is an another widely used PWM controller IC that offers adjustable switching frequency, dead time control, error amplifier and multi-topology support. You can find them in may type of commercial products such as Computer SMPS, Chargers, Inverters and many other. Their versatility makes them the best option for may applications where PWM control is used.
The TL494 has a maximum switching frequency of 300KHz with a Maximum duty cycle of 45%. The TL494 provided a push pull output with a maximum gate drive current of 0.2A. Because of the low gate drive current, they often used with external driver circuits for higher power applications. The TL494 can operate I either single-ended or push-pull modes. TL494 also features two error amplifiers, which can be used to implement current and voltage limit circuits.TL494 also offers features such as variable dead time control, internal voltage reference and internal circuitry to prevent double pulse at the outputs. TL494 is available in four different packages, PDIP 16, SOIC 16, SOP 16 and TSSOP 16.
TL594
TL594 is an upgraded version of the TL494. It has features as TL494 and some additional features. It features a maximum switching frequency of 300KHz with a maximum duty cycle of 45%. TL594 also o=offers a maximum gate drive current of 0.2A. It also feature two error amplifiers , on-chip adjustable oscillator, dead time control comparator and an internal voltage reference same as the TL494. The main differences are the accuracy of voltage reference (1% compared to 5% of TL494) and additional under voltage lock out protection with a threshold (on/off) of 6.1/6v. TL594 is also available in four different packages, PDIP 16, SOIC 16, SOP 16 and TSSOP 16.
SG3525
The SG3525 is a PWM controller designed for improved performance and minimal external components. The internal 5.1V voltage reference office and accuracy of ±1 %. It has a maximum switching frequency of 500KHz and a maximum duty cycle of 49%. It also features undervoltage lockout with threshold (on/off) of 7/6.5V. It offers a gate drive current of 0.4A. It also has features such as adjustable switching frequency (100hZ – 500KHz), current limit, dead time control, error amplifier, soft start and synchronization pin. The SG3525 also supports multi topology, such as Boost, Buck, Flyback, Forward, Full bridge, Half bridge and Push pull. Similar to TL494 , the SG3525 is also used widely and available in two packages, PDIP 16 and SOIC 16.
IR2153
IR2153 is another popular SMPS controller with fixed frequency mode operation. It combines a PWM controller with built in 600V half-bridge driver in a single package. The IR2153 is capable of handling maximum input voltage of 600V and a maximum output current of 500mA. It has a high switching frequency of 100Khz and a maximum duty cycle of 50%. It also features an under voltage lockout with a threshold (on/off) of 9/8V. Other than that, the IR2153 also features ESD protection on all pins along with many other features. The IR2153 is available in two different packages, PDIP 8 and SOIC 8.
VIPER22A
The VIPER22A from the STMicroelectronics is an another popular SMPS controller. It combines a dedicated current mode PWM controller with high voltage power MOSFET in the same package. It operates at a fixed frequency of 60KHz. It offers a maximum input voltage of 30V and a maximum output current of 0.5. The VIPER22A has features including current limiting, soft-start, and overvoltage safety. It is available in DIP 8 and SO 8 packages.
TNY268
TNY268 is a popular PWN controller from power integrations with built-in high voltage MOSFET rated up to 700V. It also features built in oscillator, current limit, and thermal protection. The TNY268 operates at frequency of 132KHz with a maximum duty cycle of 65%. Fully integrated auto-restart for short circuit and open loop fault protection – saves external component costs. Programmable line undervoltage detect feature prevents power glitches. It is available in DIP 8 and SMD 8 packages.
We have only covered a few popular PWM controller chips. You can find details about many other controllers along with other components in Components101.