TMCM-1617-GRIP-REF: Open Source Integrated Hardware Reference Design for Faster Development of End-of-Arm Tooling
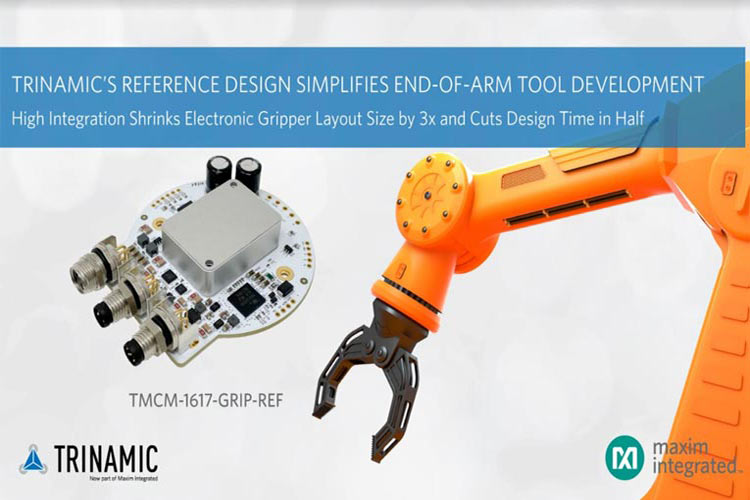
TRINAMIC Motion Control has introduced the TMCM-1617-GRIP-REF, an open-source, fully integrated reference design that simplifies the development of industrial robotic end-of-arm tooling (EoAT). By integrating hardware-based field-orientated control (FOC) and three communications ports, the new reference design reduces the design size of the electronic robotic grippers by three times and reduces the development time by half.
The TMCM-1617-GRIP-REF reference design includes Maxim Integrated's industrial-grade MAX22000 high-precision configurable analog input/output and MAX14906 quad-channel digital input/output to adjust the multiple modes of the Trinamic TMCM-1617 single axis servo driver. This reference design was developed to support industrial EtherCAT, IO-Link, or RS-485 communication and to provide software programmable analog and digital input/outputs.
Designed to fit within the standard form-factor, the device can be configured using the Trinamic Motion Control Language Integrated Development Environments (TMCL-IDE). The compact solution that measures 4197 mm2 offers adjustments of various TMCM-1617 servo drive modes including gripper position and gripping force, boost flexibility for higher factory throughput.
Features of TMCM-1617-GRIP-REF Reference Design
- Single-axis BLDC servo driver for up to 2.5 A RMS motor current
- +24 V Nominal Supply Voltage (+20 V to +28 V)
- Digital Hall sensor interface
- ABN encoder interface
- 4 Digital +24 V I/O (high side switch, push-pull driver, or a Type 1 and 3, or Type 2 digital input)
- 1 Analog output (±12.5 V output voltage range, or ±25 mA or ±2.5 mA output current range)
- 1 Differential analog input (±15 V, ±2.5 V, ±500 mV, ±250 mV, and ±125 mV input voltage ranges)
Note: More technical information can be found in the TMCM-1617-GRIP-REF Datasheet linked at the bottom of this page and on the TMCM-1617-GRIP-REF product page.