Portable and powerful, the Analog Discovery 3 is your all-in-one USB test and measurement lab.
Basics of Stepper Motors: Types, Working Principles, and Applications
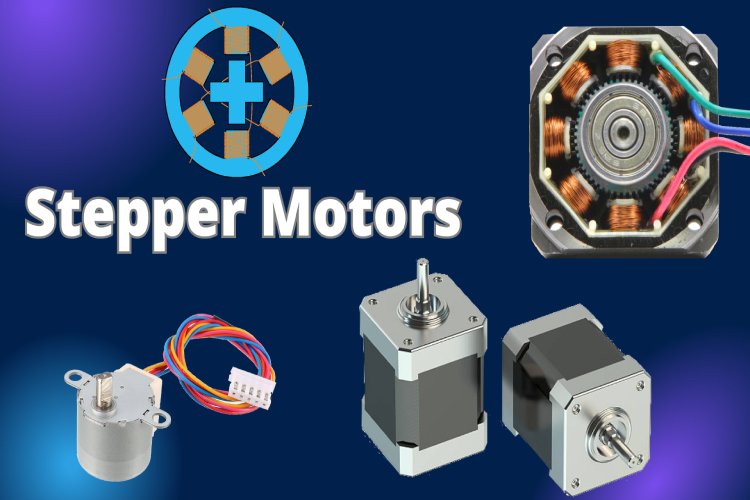
Stepper motors are a critical electromechanical component, which can be found in many everyday devices such as printers, cameras, ATMs etc. Understanding the basics of stepper motors entails delving into their various types, the underlying principles governing their operation, and the diverse array of applications they serve across industries. From robotics to 3D printing and CNC machines, the versatility of stepper motors makes them indispensable in countless automated systems where controlled motion is very crucial. In this article, we will cover the basics of stepper motors, their working principles, construction, control methods, uses, and types.
What is a Stepper Motor?
A stepper motor is an electromechanical device used for converting electrical pulses into precise mechanical motion. Unlike conventional motors, which continuously rotate when power is applied, stepper motors move in discrete steps. This ability to move incrementally makes them well-suited for applications requiring precise control over positioning and speed.
Stepper Motor Working Principle
The stepper motor diagram shows the internal structure of a stepper motor.
Stepper motors consist of a rotor and stator, with the rotor typically composed of permanent magnets and the stator containing coils of wire. By energizing these coils in a specific sequence, the magnetic field generated causes the rotor to move in precise increments, step by step. The number of steps per revolution, known as the motor's step angle, depends on its design and construction.
The fundamental operating principle of a stepper motor is as follows: When one or more phases of the stator are energized, a magnetic field is induced by the current flowing through the coil, causing the rotor to align with this field. Sequentially supplying different phases results in the rotor rotating by a precise angle to achieve the desired final position. The diagram above illustrates this principle. Initially, coil A is activated, aligning the rotor with the magnetic field it generates. Upon energizing coil B, the rotor rotates clockwise by 60° to align with the newly induced magnetic field. The same rotational movement occurs when coil C is energized. The colors of the stator teeth in the images indicate the direction of the magnetic field produced by the stator winding.
Stepper Motor Types
Stepper motors exhibit diverse types and constructions, each tailored to specific application demands. Among the prevalent variants are Permanent Magnet Stepper Motors, Variable Reluctance Stepper Motors, and Hybrid Stepper Motors.
Permanent Magnet Stepper Motors integrates a permanent magnet rotor alongside a stator adorned with electromagnetic coils. During operation, the energized coils induce alignment between the rotor's teeth or poles and the stator. Recognized for their commendable torque output, PM motors suit applications requiring moderate precision.
Variable Reluctance Stepper Motors features a rotor distinguished by salient teeth and a stator housing electromagnetic coil. Operational efficiency stems from the rotor's tendency to seek the path of least reluctance, thereby aligning with the energized stator pole. With this type of motor, it is easier to reach a higher speed and resolution, but the torque it develops is often lower and it has no detent torque.
Hybrid Stepper Motors This particular rotor design exhibits a hybrid construction, combining features from both permanent magnet and variable reluctance variants. The Rotar of hybrid motor has two caps with alternating teeth and is magnetized axially. This configuration allows the motor to have the advantages of both the permanent magnet and variable reluctance versions, such as high resolution, speed, and torque. This higher performance requires a more complex construction, and that can lead to a higher manufacturing cost. Consequently, they find Favour in diverse applications such as CNC machines, 3D printers, and robotic systems.
Unipolar and Bipolar Stepper Motors
Unipolar Stepper Motors:
Unipolar stepper motors feature a stator with center-tapped windings, allowing current flow in one direction through each winding. They typically have four or five wires, with each coil divided into two halves. Unipolar motors are simpler to control as they only require switching the polarity of one winding to generate movement. However, they tend to have lower torque compared to bipolar motors.
In operation, unipolar motors energize one half of each coil at a time, creating a magnetic field that interacts with the permanent magnet rotor. This sequential energization produces a stepwise rotation of the rotor. Unipolar motors are commonly used in applications where high precision and torque are not critical, such as small-scale automation, hobby projects, and consumer electronics.
Bipolar Stepper Motors:
Bipolar stepper motors feature two independent windings per phase, with no center tap. They typically have four wires, one for each end of the two windings. Unlike unipolar motors, bipolar motors require the reversal of current flow through each winding to generate movement. This makes their control circuitry more complex but allows for higher torque output and efficiency. During operation, bipolar motors energize each winding with current flowing in one direction, then reverse the current to create a magnetic field that interacts with the rotor. This bidirectional current flow results in a more straightforward torque production mechanism compared to unipolar motors. Bipolar stepper motors are commonly used in applications requiring higher torque and precision, such as CNC machines, 3D printers, and industrial automation. Stepper motors are commonly used in various industries, including robotics, automation, 3D printing, CNC machines, and more, where precise motion control is essential.
Stepper Motor Driving Techniques
Stepper motors employ various driving techniques to achieve precise control over their movement. These techniques include wave mode, full-step mode, half-step mode, and microstepping.
In wave mode, only one phase of the motor is energized at a time, resulting in a stepwise movement of the rotor. For example, in a two-phase motor, current flows through phase A in one direction, causing the rotor to align with its magnetic field. Subsequently, phase B is energized, rotating the rotor by 90° to align with its magnetic field. This process repeats, alternating between phases A and B, with changes in current direction determining the rotor's movement direction.
Full-step mode energizes two phases simultaneously, providing increased torque output compared to wave mode. This mode follows a similar stepwise movement pattern, but with both phases active at each step, generating a stronger magnetic field and torque.
Half-step mode combines aspects of wave and full-step modes, reducing the step size by half (e.g., from 90° to 45°). While offering finer resolution, torque output fluctuates as it is higher when both phases are active and weaker when only one phase is energized.
Microstepping enhances resolution further by controlling current intensity in each phase, allowing for even smaller step sizes. This technique involves incrementally varying current levels to achieve intermediate rotor positions between full steps. While microstepping enables high position resolution, it necessitates more complex motor driver circuitry and reduces torque output per step due to smaller step sizes.
Stepper Motors vs Servo Motors
Stepper motors and servo motors are both widely used in motion control applications, but they have distinct characteristics and are suited for different types of tasks. Here's a comparison between the two:
1) Control Method:
Stepper Motors: Stepper motors move in discrete steps, with each step corresponding to a specific input pulse. They do not require feedback to determine their position, making them simpler to control in open-loop systems. Servo Motors: Servo motors operate based on feedback from an encoder or resolver, allowing for precise control of position, velocity, and torque. They are commonly used in closed-loop control systems to achieve accurate and dynamic motion control.
2) Precision and Accuracy:
Stepper Motors: Stepper motors provide precise positioning and repeatability, making them suitable for applications where accuracy is essential, such as 3D printing, CNC machining, and robotics. Servo Motors: Servo motors offer higher precision and accuracy than stepper motors, especially in closed-loop systems where feedback is used to correct errors in position or velocity. They are commonly used in applications requiring tight tolerances and high performance, such as industrial automation and robotic arms.
3) Torque and Speed:
Stepper Motors: Stepper motors typically provide high holding torque at low speeds, but their torque drops off at higher speeds. They are well-suited for applications requiring high torque at low speeds, such as positioning and holding loads. Servo Motors: Servo motors can provide high torque over a wide range of speeds, making them ideal for dynamic applications that require precise control of acceleration, deceleration, and velocity.
4) Complexity and Cost:
Stepper Motors: Stepper motors are simpler and less expensive than servo motors, as they do not require feedback devices or complex control algorithms. They are often preferred for cost-sensitive applications or projects with simpler motion control requirements. Servo Motors: Servo motors are more complex and typically more expensive than stepper motors due to the additional components required for closed-loop control. However, they offer superior performance and versatility in demanding motion control applications.
In summary, stepper motors are suitable for applications requiring precise positioning and simple motion control, while servo motors excel in tasks that demand high precision, dynamic performance, and closed-loop control. The choice between stepper and servo motors depends on factors such as the application requirements, performance expectations, and budget constraints.
Stepper Motor Applications
Stepper motors find applications across a wide range of industries and technologies due to their precise control and ability to convert digital pulses into mechanical motion. Some common applications include:
- CNC Machines: Stepper motors are extensively used in Computer Numerical Control (CNC) machines for controlling the movement of the cutting tool along multiple axes with high accuracy. They enable precise positioning and repeatability in tasks such as milling, engraving, and 3D printing.
- 3D Printers: Stepper motors drive the movement of the print head and build platform in 3D printers, allowing for precise layer-by-layer deposition of material to create complex three-dimensional objects with accuracy and consistency.
- Robotics: Stepper motors are utilized in robotic systems for controlling the movement of robotic arms, grippers, and other components. Their ability to move in precise increments facilitates tasks such as pick-and-place operations, assembly, and positioning in industrial and collaborative robot applications.
- Medical Equipment: Stepper motors play a vital role in medical devices and equipment, including medical imaging systems (e.g., MRI and CT scanners), robotic surgery systems, infusion pumps, and laboratory automation. They enable precise movement and positioning of components critical for diagnostics, treatment, and research.
- Automotive Systems: Stepper motors are employed in various automotive applications, such as fuel injection systems, electronic throttle control, HVAC (Heating, Ventilation, and Air Conditioning) actuators, and headlamp leveling systems. They provide accurate control over functions requiring precise positioning and movement.
- Textile Machinery: In textile manufacturing, stepper motors drive the movement of yarn feeders, needle bars, and other components in knitting, weaving, and embroidery machines. Their precise control allows for intricate pattern designs and adjustments in fabric production.
- Consumer Electronics: Stepper motors are used in consumer electronics devices such as digital cameras, printers, scanners, and disk drives for controlling the movement of lenses, paper feeds, and read/write heads. They enable precise positioning and movement in compact and portable devices.
- Automation and Control Systems: Stepper motors are integrated into various automation and control systems for tasks such as conveyor belt positioning, packaging, labeling, and material handling in manufacturing facilities, warehouses, and logistics centers.
Popular Stepper Motors
Stepper motors are widely used in various industries and applications due to their precise control and reliability. Some of the most commonly used stepper motors include:
- NEMA 17: NEMA 17 stepper motors are versatile and widely used in 3D printers, CNC machines, robotics, and automation applications. They offer a good balance between torque, size, and cost, making them suitable for a wide range of projects.
- NEMA 23: NEMA 23 stepper motors are larger and more powerful than NEMA 17 motors, making them suitable for applications that require higher torque and performance, such as larger CNC machines, industrial automation, and motion control systems.
- NEMA 34: NEMA 34 stepper motors are even larger and more powerful than NEMA 23 motors, making them ideal for heavy-duty applications that require high torque and precision, such as large-scale CNC machines, industrial robotics, and manufacturing equipment.
- NEMA 14: NEMA 14 stepper motors are smaller than NEMA 17 motors but offer comparable performance. They are commonly used in applications where space is limited, such as compact 3D printers, scanners, and medical devices.
- 28-BYJ48: Known for its affordability and ease of use, the 28-BYJ48 stepper motor is popular in hobbyist projects, small-scale automation, and low-cost applications. It's commonly found in Arduino-based projects and DIY kits.
Popular Stepper Motor Drivers
Stepper motor drivers play a crucial role in controlling the movement and performance of stepper motors. These drivers serve as intermediary devices between the motor and the control system, translating electrical signals into precise motion. Popular stepper motor drivers include the ULN2003, DRV8825, TMC2209, A4988, TMC2208, TB6600, and TMC5160, each offering unique features and capabilities suited for various applications.
- ULN2003: This is a widely used and cost-effective driver commonly found in low-power applications. It is suitable for driving small to medium-sized stepper motors with basic control requirements.
- DRV8825: Known for its high current capability and microstepping support, the DRV8825 offers precise control over stepper motors. It is favored in applications requiring smooth motion and high torque output.
- TMC2209: Part of the Trinamic StealthChop family, the TMC2209 driver excels in providing quiet and efficient operation. It offers advanced features such as stall detection and sensorless homing, making it popular in 3D printers and other motion control systems.
- A4988: Another popular choice, the A4988 driver offers a balance of performance and affordability. It supports microstepping and is commonly used in hobbyist projects, 3D printers, and CNC machines.
- TMC2208: Similar to the TMC2209, the TMC2208 driver is known for its quiet operation and advanced features such as stealthChop2 and spreadCycle. It is often used in applications where noise and efficiency are critical factors.
- TB6600: The TB6600 is a robust driver capable of driving high-power stepper motors with ease. It offers adjustable current settings and protection features, making it suitable for industrial applications and high-performance setups.
- TMC5160: The TMC5160 is a high-performance driver featuring advanced current control algorithms and diagnostic capabilities. It is ideal for demanding applications requiring precise motion control and high reliability.
If you want to know how to use a stepper motor with Arduino, please check out the Arduino Stepper Motor article.