MCX W: Bluetooth LE, Zigbee, and Matter over Thread multiprotocol MCUs
Tin Solder, Lead Solder, Flux-core Solder, and Rosin-core Solder– Differences and Uses
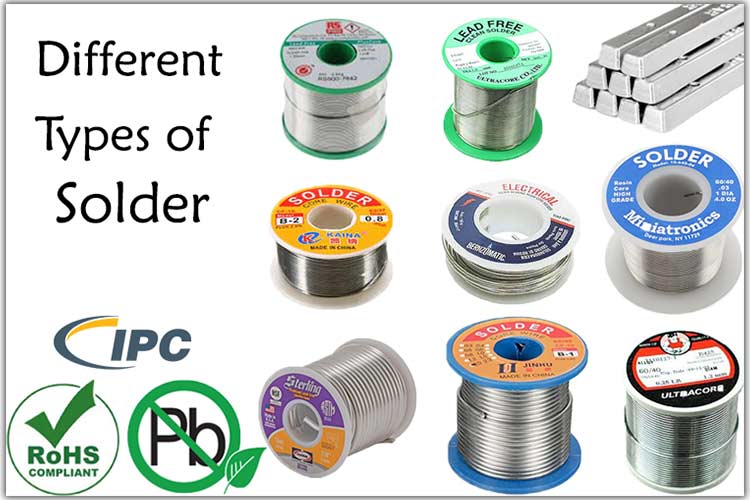
Soldering is the backbone of modern electronics manufacturing and repair, ensuring reliable connections between components on circuit boards and wires. However, not all solder wires are created equal. Understanding the various types of solder and their specific applications is essential for achieving high-quality, durable connections. Let's delve into the diverse world of solder used in electronics and their respective uses.
Even though we mostly relate soldering to electronics, it is a fundamental process in many other areas such as plumbing, jewelry making, and various other industries where metal joining is required. Different types of solder are available to suit specific applications, each with its own composition, melting point, and characteristics. Let's explore the various types of solder and their uses:
Leaded Solder: Lead solder, once common in electronics and plumbing, has been phased out due to environmental and health concerns associated with lead exposure. It typically consists of a mixture of tin and lead and has a low melting point, making it easy to work with.
Hard Solder (Silver Solder): Hard solder, also known as silver solder or silver brazing, is used for joining metals that require high-strength and durable joints. It contains silver as a primary component and requires high temperatures for melting, making it suitable for applications where mechanical strength is crucial.
Indium Solder: Indium solder is a type of solder that contains indium as the primary component. It is commonly used in applications requiring low-temperature soldering, such as bonding electronic components with sensitive materials or substrates.
Lead-Free Solder: Lead-free solder has become the standard in electronics manufacturing due to environmental and health concerns associated with lead-based solder. They are also called silver alloy solder and are typically composed of tin, silver, and copper (Sn-Ag-Cu), lead-free solder offers excellent reliability and meets stringent regulatory requirements.
Gold Solder: Gold solder contains gold as a primary component and is used in jewelry-making and electronic applications where a high-quality, corrosion-resistant joint is required.
Tin Solder: Tin solder is composed primarily of tin and is commonly used in electronics and plumbing applications. It offers good conductivity and is often used for soldering copper pipes and electrical wires.
Solder Wire vs Solder Bar
Solder wire and solder bar are the two common forms of solder used in various applications, each offering unique advantages depending on the task at hand.
Solder Wire: Solder Wire is a flexible and convenient form of solder that comes in spools or coils. It is widely used for hand soldering tasks, offering precise control over the amount of solder applied to joints. Solder wire typically contains a core of flux, which helps clean the surfaces being soldered and promotes better adhesion. This makes solder wire ideal for intricate soldering work, such as joining electronic components on circuit boards or repairing delicate electrical connections. Its flexibility and ease of use make it a preferred choice for most soldering applications.
Solder Bar: Solder Bar, on the other hand, is a solid form of solder typically used in industrial applications or for soldering large components. It comes in the form of solid bars or sticks and requires melting using a solder pot or furnace. Solder bars are advantageous for bulk soldering operations or when joining larger metal pieces that require a significant amount of solder. They provide a consistent supply of solder and are suitable for applications where precision is less critical compared to solder wire. Solder bars are commonly used in soldering plumbing fittings, metalwork, and certain manufacturing processes.
Type of Solder Based on Different Core
The solder wire you commonly see has a hollow core inside, you can say the solder wire is a tube-like structure, inside this tube, there can be different materials, and depending upon the material, it is differentiated into four categories a list of those is given below.
Uncored Solder: Plain solder without a flux or rosin core. Usually difficult or tedious to work with, since it requires joints to be well-fluxed before application.
Rosin core solder: Rosin is a resin obtained from coniferous plants which are boiled down to remove volatile compounds. It is typically used as solder flux and is found inside solder wire as a core. Multiple cores per wire are also available. Rosin generally leaves behind residue which must be cleaned up.
Flux core solder: Flux-cored solder contains single or multiple cores of flux. Flux is somewhat more acidic than rosin, so the residue must be washed off to prevent further damage to joints and surrounding components.
Acid core solder: Acid core solder consists of an acid-based flux, which is a strong and more aggressive form of solder flux. This type of solder helps to prevent the formation of an oxide layer that is harmful to the surface. Acid core solder is most often used in plumbing applications.
Leaded and Lead-Free Solder & their Compositions
As we mentioned at the start leaded and lead-free solder are the most popular and most commonly used type of solder in the electronic industry. So, let’s check them out a little more closely.
Lead-Based Solder:
Leaded solder is the most common type of solder. It contains the metal Lead. Generally, leaded solder is considered the best, because of its good wetting and mechanical properties. A list of the most common types of lead-based solder is given below.
60/40 – It is perhaps the most well-known and ubiquitous type of lead solder; it consists of 60% Tin and 40% Lead. It melts at around 190°C and forms soft joints, leading to joints that do not crack. But if the joint is moved before the solder has time to fully melt, the resulting joint is called a ‘cold joint’ and has poor electrical and mechanical properties. It tends to break apart very easily.
63/37 – This is the eutectic counterpart of 60/40 solder, melting at precisely 183°C. This property eliminates the formation of cold joints.
50/50 – This mix is primarily used for plumbing with high melting points and low ductility.
Lead-free Solder
As the name suggests, it is devoid of lead. Instead, the solder is made mostly of tin alloyed with other metals, such as Silver and Copper. Lead-free solders are RoHS (Reduction of Harmful Substances) standard compliant and better for the environment, with the harmful effects of Lead on the environment being well known.
The most common lead-free solder alloy you can find is SAC305. It is made up of 96.5% Tin with 3% Silver and 0.5% Copper, used in SMT assembly. Next, on the list is SAC387, which is Tin with 3.8% Silver and 0.7% Copper. These are the costliest. Next, we have SAC405 which has Tin with 4% Silver and 0.5% Copper. Of the above alloys, SAC387 and SAC405 are eutectic, meaning they have the same melting and solidification point, in this case, 217°C. Meanwhile, SAC305 has a melting point between 217 - 219°C.
Comparing Properties of Similar Leaded and Lead-Free Solder:
Property | Leaded Solder | Lead-free Solder |
Composition | 37% Sn, 63% Pb | 95.5% Sn, 5% Ag, 0.5% Cu |
Melting Point | 183°C | 217°C |
RoHS Compliance | No | Yes |
Density | 8.5g/m2 | 3.7g/m2 |
Resistivity | 15mΩ-cm | 11mΩ-cm |
Sn – Tin, Pb – Lead, Cu – Copper, Ag – Silver
Important Parameters to Consider While Choosing Leaded and Lead-Free Solder:
- The general usability of Lead-Free solder is considered to be much harder than Leaded solder. The higher melting point contributes to the problem.
- The fluxes used with Lead-free solder are generally more corrosive and are more of an irritant than the fluxes used for Leaded solder and must be dealt with more carefully. They can corrode the tip of a soldering iron much faster than regular flux.
- The elevated temperatures required to work with Lead-free solder increase the amount of flux (and to a smaller extent the amount of actual metal vapor produced) which can be a health hazard.
- Solder alloys containing mainly Tin can develop whiskers over time, in a solder joint. This can lead to shorting with nearby joints.
- Lead-free solder is much less free flowing (wettable) as compared to Leaded solder, which might make soldering a lot more difficult.
Commonly Asked Questions
What kind of solder is best for electrical wire?
For electrical wire connections, a leaded solder with a rosin flux core is often preferred. This ensures good conductivity and reliability. For high gauge wires, Tin-based solders, such as SAC (tin-silver-copper) alloys, are commonly used for electrical applications due to their excellent conductivity and compatibility with various metals.
What type of solder is suitable for copper wire?
When soldering copper wire, a solder with a flux core specifically designed for copper is recommended. Look for solder wire that is formulated to work well with copper surfaces, providing strong adhesion and minimal oxidation during soldering.
How strong is solder wire?
The strength of solder wire can vary depending on its composition and application. However, solder joints made with proper soldering techniques can provide reliable mechanical strength. For most electronic and electrical applications, solder joints are strong enough to withstand typical stresses encountered during use.
What kind of solder is best for SMD components?
For surface mount device (SMD) components, a solder pastes specifically designed for SMD soldering is typically used. Solder paste is a mixture of solder alloy particles and flux, often applied using stencil printing or dispensing techniques. It is designed to reflow and form strong, reliable solder joints between SMD components and circuit boards during the soldering process.
What is 44 rosin core solder?
44 rosin core solder refers to a specific type of solder wire with a composition of 60% tin and 40% lead. The "44" designation indicates the tin-lead ratio, while the rosin core provides flux for soldering. This type of solder is commonly used in electronics soldering applications, offering both ease of use and reliability. However, due to environmental and health concerns associated with lead, lead-free alternatives are increasingly favored where possible.
What is the melting point of solder?
The melting point of solder varies depending on its composition. Lead-based solders typically melt at lower temperatures, around 180°C to 190°C (360°F to 370°F), while lead-free solders have higher melting points, ranging from 220°C to 260°C (430°F to 500°F) or more. Leaded solder with a melting point of 138°C is also popular in the electronic repair industry.
What is low melt solder?
Low melt solder, also known as low melting point solder, consists of solder alloys designed to melt at temperatures significantly lower than standard solder compositions, typically ranging from around 50°C to 150°C (122°F to 302°F). These alloys often incorporate metals such as bismuth, indium, or gallium, which lower the melting point while preserving essential soldering properties. Widely utilized in electronics assembly, low melt solder reduces the risk of thermal damage to heat-sensitive components like plastic connectors or delicate circuitry, enabling a controlled soldering process even at relatively low temperatures.
Conclusion
For hobbyists, Leaded solder is much more convenient since it is the easiest to work with. The experience of working with Lead-free solder depends on the quality of the product. It is also important to have a flux-cored solder, this will make soldering much easier. Flux-cored is preferred over rosin-cored since it’s easier to clean up.