Portable and powerful, the Analog Discovery 3 is your all-in-one USB test and measurement lab.
How to do Spread Control on Stepper Motors to Improve Precision and Smoothness
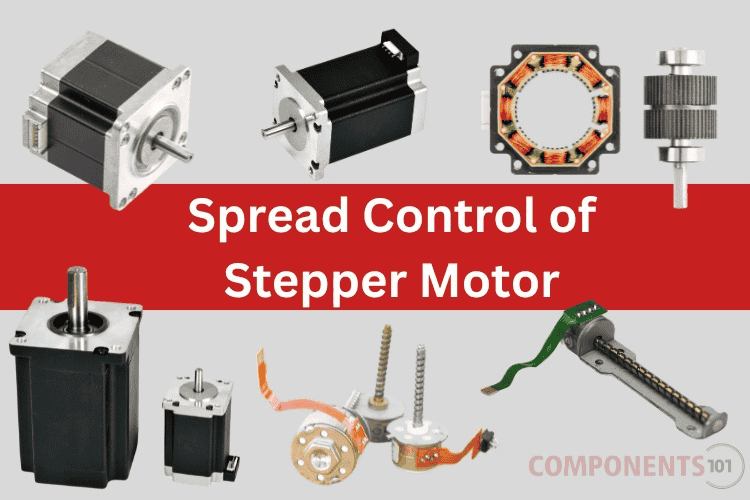
Stepper motors are essential for many modern-day applications, from 3D Printers and CNC Machines to Robotics, where precision movements are required. They are known for their discrete step movements, which provide an advantage in positioning tasks. However, achieving smoother and more precise control requires more than just standard stepping techniques. This is where spread control comes into play, allowing the stepper motor's movement to be divided into smaller, more gradual steps. This results in finer motion and improved accuracy beyond the motor's typical full-step size.
What is Microstepping?
Microstepping is a technique that refines the stepper motor's movement by dividing each full step into smaller increments. Unlike full-step and half-step modes, which involve moving the motor in larger, more discrete steps, micro-stepping allows the motor to take much finer steps. This results in improved positioning accuracy and reduced vibrations.
Microstepping works by adjusting the current in the motor windings more precisely, usually with the help of sine or cosine waveforms. These waveforms enable the motor to move incrementally, smoothing out the motion and making transitions less abrupt.
The Role of Spread Control in Microstepping
Spread control refers to the sophisticated management and distribution of micro-stepping signals to optimize motor performance. Instead of making abrupt transitions between step positions, the control system gradually adjusts the current through the motor windings. This gradual adjustment, or spreading, occurs across multiple microsteps.
By implementing spread control, the motor's motion becomes smoother and more continuous. In the above image, you can see the difference between normal driving and Microstepping. This technique helps minimize torque ripple, which is the variation in torque output as the motor steps through its positions. Torque ripple can cause vibrations and noise, which are particularly noticeable at low speeds. Spread control mitigates this issue by ensuring that the motor transitions smoothly between steps, thereby enhancing overall performance.
Understand MicroStepping with Nema17 as Example
The NEMA 17 is a popular stepper motor size used in various applications, including 3D printers, CNC machines, and robotics. It is named for its 1.7-inch (43.2 mm) faceplate size and is known for its reliable performance and versatility. Let’s consider this NEMA 17 as an example to understand the difference between stepping modes.
-
Full-Step Mode: The NEMA 17 motor moves 1.8° per step, resulting in 200 full steps per revolution. This mode provides relatively high torque but, as a drawback, vibrations and less smooth movement can be observed.
-
Half-Step Mode: In half-step mode, the motor alternates between full steps and half steps, effectively doubling the resolution to 0.9° per step. This provides smoother motion but still has some limitations in precision.
-
Microstepping Implementation: Microstepping divides each full step into smaller increments. For example, with a 16x micro-stepping mode, each full step is divided into 16 smaller steps, resulting in a step angle of 0.1125° (1.8° / 16). This allows for spread control over the motor's movement.
With all this theory, let’s move on to the implementation.
Two Ways to Implement Microstepping with Stepper Motors
When it comes to implementing micro stepping with stepper motors, there are a couple of approaches worth considering. These are not the only ways to go about it, but they’re good starting points.
First Approach: Direct Microcontroller Control
One method involves using a microcontroller to directly manage the motor. In this case, the microcontroller itself generates the microstepping waveforms that control the motor’s movement. This approach can be a bit more complex since it requires programming and hardware skills, but it gives you full control over how the motor behaves.
By generating waveforms—typically sine or cosine waves—you can finely control the current flowing through the motor windings. You might use Pulse Width Modulation (PWM) or a Digital-to-Analog Converter (DAC) to adjust the current levels as needed. In this setup, each step of the motor is broken down into smaller increments, allowing for finer movements.
Benefits: With this approach, you have complete control over the motor, which can be beneficial if you need to adjust the behavior dynamically or implement advanced features. It’s great for projects where you need precision and real-time control.
Where It’s Useful: This method is ideal for high-precision applications, such as robotics or automation systems, where custom motor control is crucial.
Second Approach: Using a Stepper Motor Driver
Another way to go about it is by using a dedicated stepper motor driver chip (eg: TMC2208). These chips handle the heavy lifting for you—they take care of the current regulation needed for micro-stepping internally. All you need to provide are simple step and direction signals, and the driver does the rest. You can also select the stepping mode (e.g., full step, half step, 1/8 step, 1/16 step) by adjusting specific pins on the driver.
Benefits: This approach is much easier to implement since the driver manages all the complex aspects of current control. You don’t need as much coding, and you can still achieve smooth motor operation with different step resolutions. It’s a great option for applications like 3D printing or CNC machines.
Where It’s Useful: This method is best for projects where ease of use is a priority, and you don’t need highly customized motor control.
Conclusion
In applications where precision, smoothness, and quiet operation are critical, spread control plays a vital role in optimizing stepper motor performance. By implementing micro-stepping, either through direct control using a microcontroller or with the help of dedicated stepper motor drivers, you can finely manage the motor's movements. This helps in reducing torque ripple, minimizing vibrations, and achieving finer resolution beyond standard stepping modes.
For those who need complete control over the motor's behavior, direct microcontroller control offers unparalleled flexibility, allowing for advanced customization. On the other hand, using a stepper motor driver simplifies the implementation, handling the complexities of current regulation while still providing smooth and accurate motion. Both approaches have their strengths, and the right choice depends on the specific needs of your project, whether it's ease of use or precision control.
Spread control, in essence, is about optimizing the stepper motor’s performance, ensuring that it operates smoothly and efficiently across a wide range of applications, from robotics and automation systems to 3D printing and CNC machining.